Structural Foam for Injection Molding
What is Structural Foam for Injection Molding?
Structural foam is a low-pressure form of injection molding, which utilizes most thermoplastics, (including post-consumer regrind), to mold rigid products, which can have thicker walls and higher stiffness-to-weight ratios than standard injection molded products.
Structural Foam Process
In the structural foam molding process, a physical or chemical blowing agent is mixed in with the resin. The resin is shot into the cavity, but not completely filled or packed out. The blowing agent expands to push the resin to the extremities of the cavities. As the part cools, the internal pressure of the foaming action takes up the internal shrinkage, and reduces sinks over ribs or heavy cross-sections.
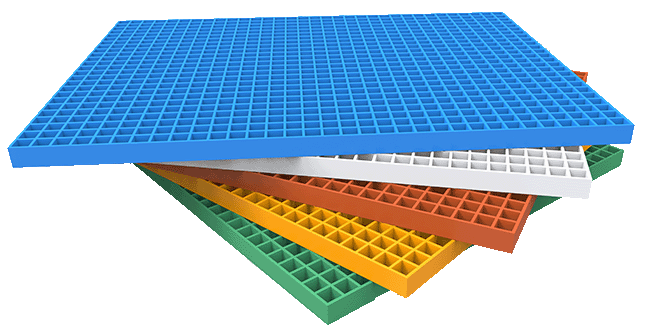
Advantages of the Structural-Foam process:
There are many advantages of the structural foam injection molding which combine to provide an economical advantage over other processes, and allow production of parts which can’t be matched by any other process. Following is a list of many of the advantages of the structural foam molding process:
- Low cost tooling with the same molded-in detail and features possible in standard injection molding
- Multiple parts and multiple tooling can be run on a single machine.
- Two different materials and or two different colors can be run at the same time.
- Product can easily be gated at multiple points on the part, which can be strategically positioned to optimize filling, and processing.
- The molding process utilizes low-pressure to mold the parts which results in low stress and warpage in the parts.
- The low pressure part of the process allows molding of large parts with low machine tonnage.
- The process allows a wide range of design flexibility.
- Superior part and process repeatability are possible with the process.
- High strength-to-weight ratio.
- Reduced part weight while maintaining high stiffness-to-weight ratio.
- Can mold medium wall thickness through very thick wall sections with minimal sink marks.
- Reduced weight of 10 to 20% over solid plastic part.
- Total shot weight of up to 200 pounds.
- * PRL PPX SF1
- * PRL PPX SF2
- * PRL PC SF FR
- * PRL PC SF FR1
- * PRL PC SF FR G20
- * PRL PC SF FR G30
- * PRL TP SF G10
- * PRL TP SF G30
- * PRL TP SF FR G10
- * PRL TP SF FR G30
- Easy Flow FR PPE/PS Blend
- Standard Flow FR PPE/PS Blend
- 5% Glass Filled FR Polycarbonate
- 10% Glass Filled FR Polycarbonate
- 20% Glass Filled FR Polycarbonate
- 30% Glass Filled FR Polycarbonate
- 10% Glass Filled PBT
- 30% Glass Filled PBT
- 10% Glass Filled FR PBT
- 30% Glass Filled FR PBT
Additives, Modifiers, and Reinforcing Agents:
- Additives – UV stability, easy release (mold releases), colorants, and other stability additives
- Modifiers – Flame retardants, impact modifiers, flow enhancers
- Reinforcing Agents – Glass fibers, mineral fillers
PRODUCT Q&As
Q. What is structural foam?
Q. How is structural foam made?
Structural foam molding minimizes molded-in stress that can lead to warpage and part deformation. Other advantages include less energy usage due to the low-pressure process and cost savings and sustainability from using less resin and less-expensive aluminum tooling. Also, versatility in part geometry, from thin walls to very thick and large shapes, is an additional benefit of using structural foam. Aesthetically, the foaming bubbles in the matrix pack out the resin and reduce the incidence of sink on the exterior show side of the plastic part.
Q. What are the drawbacks to using structural foam in injection molding?
Q. What applications is structural foam used for?
Our Mission
My mission at Polymer Resources has not changed since I founded this company more than four decades ago. It includes continuing our tradition of financial stability, sustainable growth and visionary leadership that compounds success for customers, suppliers and employees. It also means proudly manufacturing our products in America, and making them available to the global marketplace.
Les Klein, Chief Executive Officer, Polymer Resources, Ltd.
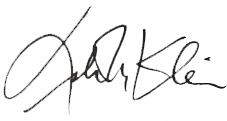